Introduction
Challenges in Curved Surface Printing
Cups, bottles, and various shapes use curved surface printing during production. High precision, efficiency, and stability are essential for this process. They ensure high-quality production and a smooth manufacturing workflow. Traditional techniques struggle with material stability and efficiency. They also waste a lot of resources. Accurate product positioning is a significant challenge when printing on curved surfaces. Traditional product feeding systems don’t align products with precision. This leads to print defects and poor positioning. Conventional drive systems have power and speed changes. These variations lead to uneven print quality and more product rejections.
Traditional printing methods waste a lot of materials. They often create many rejected prints. Misalignments and misprints waste materials. This causes extra costs and lowers manufacturing efficiency. Printing technology has advanced with new feeding mechanics and drive systems. This change has helped solve production challenges.
Innovation in Printing Technology
Spiral decomposition feeding and servo motors changed curved surface printing. They helped shape the technology we use today. Technology’s modern improvements fixed the weaknesses of standard systems. This created a more reliable and efficient solution.
Spiral decomposition feeding is a method that separates products. This ensures they are ready for controlled distribution to the printing station. Print quality gets better with servo motors. They help maintain accuracy and reduce misalignment during printing. Manufacturers who combine these technologies can create an automated printing process. This process offers flawless operation and boosts production rates.
The Principle and Advantages of Spiral Decomposition Feeding

How Spiral Decomposition Feeding Works
Spiral decomposition feeding uses a spiral mechanism to break up stacked products. It then feeds them into printing stations through a precise distribution process. Spiral decomposition feeding fixes problems found in push-feeding systems. It ensures that workers handle materials well, preventing product jams and inconsistencies.
The system uses a spiral feeding mechanism. This helps with product spacing and flow control. A spiral feeding mechanism aligns items in the correct position. This prevents overlaps, reducing the chance of print errors and material damage.
Key Benefits
- This method uses controlled feeding. It boosts productivity and speeds up manufacturing.
- Spiral decomposition feeding boosts printing reliability. It cuts down on material jamming and lowers the chances of equipment misalignment.
- Spiral decomposition feeding works well with many product forms and materials. It handles various cup and bottle shapes and other curved surfaces.
- The feeding system uses automation. This allows for semi-autonomous operations and reduces manual labor costs.
The Role of Servo Motors in Curved Surface Printing
Features of Servo Motors
Modern printing systems use servo motors. These motors provide accurate position control and smooth motion during printing. These motors offer:
- Servo motors are accurate. This allows for precise positioning and correct alignment of printed designs.
- The rotational speed is stable, and the torque stays consistent. This prevents print quality from getting worse.
- Servo motors provide quick printing speeds and steady accuracy. This makes them ideal for industrial manufacturing.
Applications in Rotary Table Operations
The rotary table’s operations in curved surface printing depend on servo motors. Products remain steady on the rotary table while it moves for consistent printing. Servo motors provide:
- Smooth rotation mechanisms control vibrations and sudden movements to maintain printing precision.
- Fast Adjustments let printer systems manage different speeds and complex designs. This makes them ideal for simple and detailed print jobs.
- The synergy between spiral decomposition feeding and servo motors.
Synergy Between Spiral Decomposition Feeding and Servo Motors
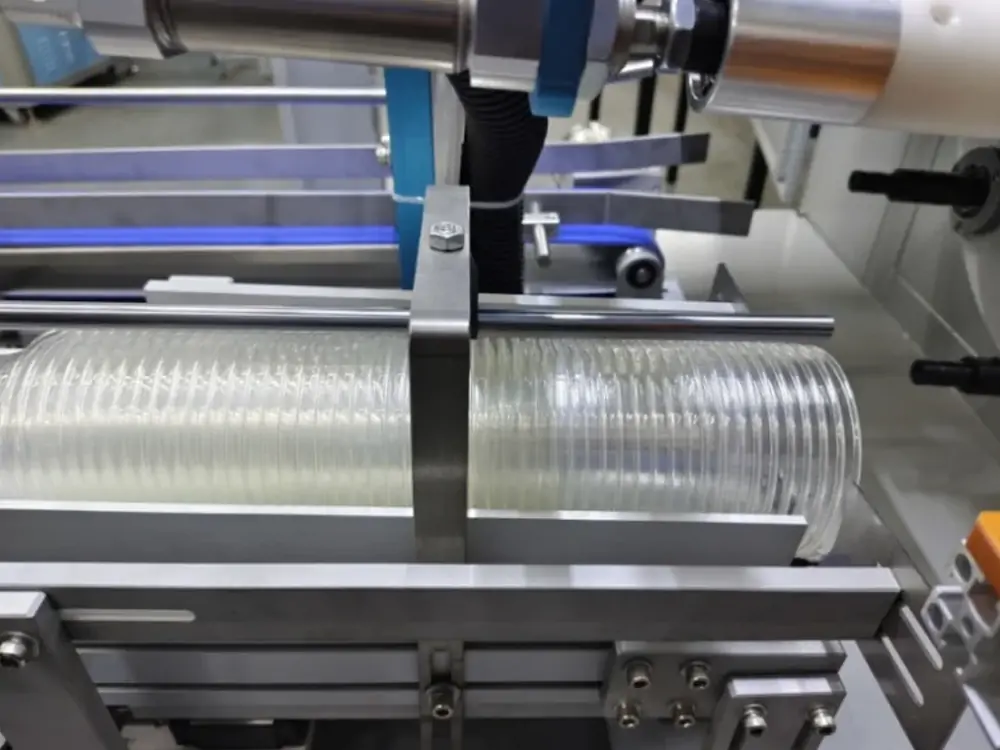
Coordinated Operation
The spiral feeding system and servo motors work together. They deliver products in order and ensure stable power connections. Their accurate placement abilities enhance efficiency. Combining both methods helps printers operate smoothly and boosts productivity.
Advantages in Practical Applications
Better stability and improved control systems lead to precise printing. This also reduces errors and cuts down on the need for reprinting. This system aids mass production. It works consistently and increases production speed. Adjusting the printer lets manufacturers expand their product range. They can offer single-color printing, multi-color options, and complex designs.
Advantages Over Traditional Technologies
Comparison with Conventional Feeding Methods
Push-feeding technology can cause product jams and misalignments. It also leads to unstable feeding speeds. Spiral decomposition feeding makes the operation more reliable. It keeps spacing consistent and stops products from overlapping.
Comparison with Traditional Drive Systems
Traditional motors lack the precision needed for good results in curved surface printing. The printing operation is inconsistent. This happens because the system changes speed and torque. Servo motors enable printing operations to function with precision and efficiency.
Customer Benefits and Real-World Applications
Improved Production Efficiency
Using servo motors with spiral decomposition makes printing operations quicker. The automated system cuts down on manual labor and reduces costs. This results in better efficiency.
Enhanced Competitive Edge
This advanced technology helps businesses manage high-volume production while meeting top-quality standards. The strategic implementation makes the product competitive through market advantages.
Case Studies
The AP-600-8 Automatic Cup Printing Machine boosted output by 30%. It also cut defects by 20%. This success comes from its spiral decomposition feeding assembly and servo motor framework. Field tests show these innovations work well in real industrial settings.
Future Developments and Applications
Advancements in technology
Future curved surface printing innovations aim to enhance feeding systems. This will help manage complex manufacturing components better. Servo motors and intelligent control systems work together. They boost automation and remove the need for human assistance during operation.
Expansion of Application Industries
Curved surface printing began in packaging and beverage production. It also serves high-end fields like healthcare, automotive, and aerospace. Precise requirements in these high-end industries demand sophisticated printing technologies as a necessity.
Conclusion
Spiral decomposition with servo motors boosts the printing of curved surfaces. This system solves the flaws of traditional methods. It provides faster operations, more reliable performance, and better print quality. The AP-600-8 Automatic Cup Printing Machine shows how technology has advanced. It offers perfect automated printing solutions for businesses.
Manufacturers should adopt these advanced systems. This is crucial for increasing productivity and staying competitive as the industry changes. The machine prints plastic cups. It works as a plastic cup maker and a print-on-cup device. The machine also prints plastic cups. It functions as a plastic cup machine and a plastic cup printing system.