The tension of a screen controls key aspects of screen printing. It affects the quality, uniformity, and accuracy of prints. It’s vital to control screen tension for printing on bottles and tubes. The curved substrates must have a high, controlled screen tension to get the best results. This work looks at good screen tension and how to achieve it in cylindrical screen printing. Screen tension is, in fact, one of the fundamentals of screen printing. It concerns the tightness of a mesh when placed on a screen printing frame. That is the correct pressure level to transfer ink from the cartridge to the paper. It prevents frost and smudged prints. This can help, especially in cylindrical screen printing. The curved surface complicates it.
Correct screen tension improves design sharpness and preserves printing screens. Printers can succeed on complex cylindrical substrates with proper screen tension. This follows the screen tension principles outlined above. Screen tension is the tension in a screen printing frame’s mesh. It is key to controlling ink flow and screen ground pressure in fabrication. Proper screen tension is vital for surfaces like bottles, tubes, or containers. Curved substrates pose unique challenges. So, it is crucial to optimize screen tension. This is key to achieving high-quality results. This article is about the best screen tension for cylindrical printing and how to achieve it.
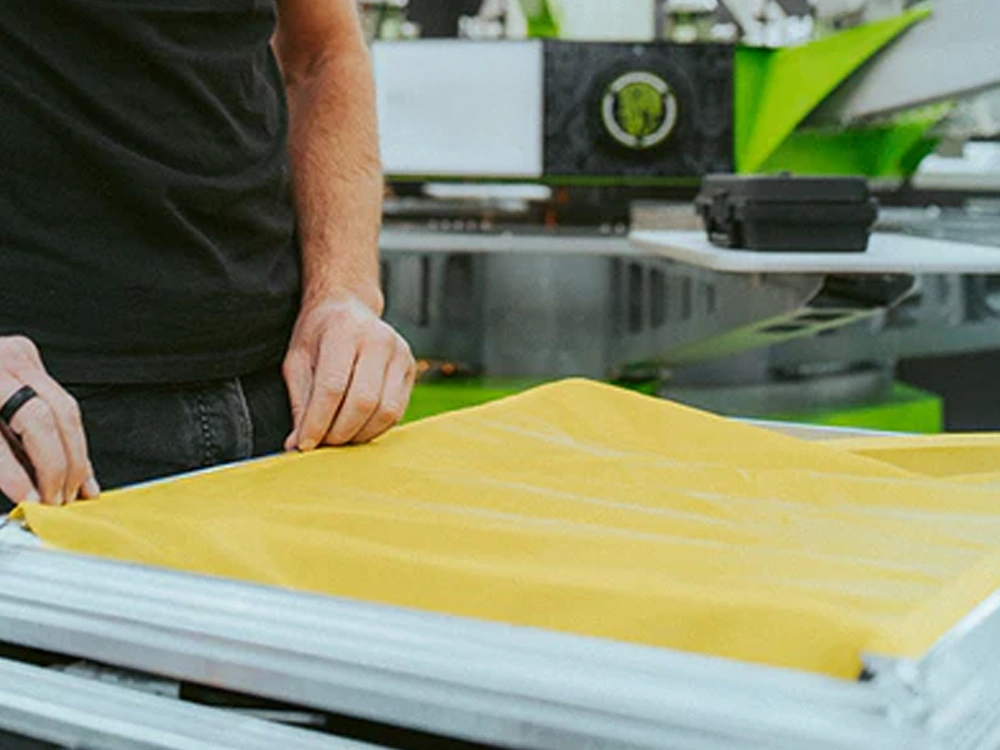
What is screen tension?
Screen tension is the tautness of the mesh on a screen printing frame. This is critical. The stress affects the screen’s ability to maintain contact with the substrate and regulate ink flow during printing.
Measuring screen tension:
There are typically two units used to measure screen tension: Newtons (N/cm). It measures the force exerted on the mesh about width to calculate its tension. An essential measure of a screen is the tension value. The higher the value, the tighter the screen. A low value means the screen will be loose. Screen tension should apply equal pressure to the emulsion, ink, and image transfer on any surface during printing. It must be appropriate for this.
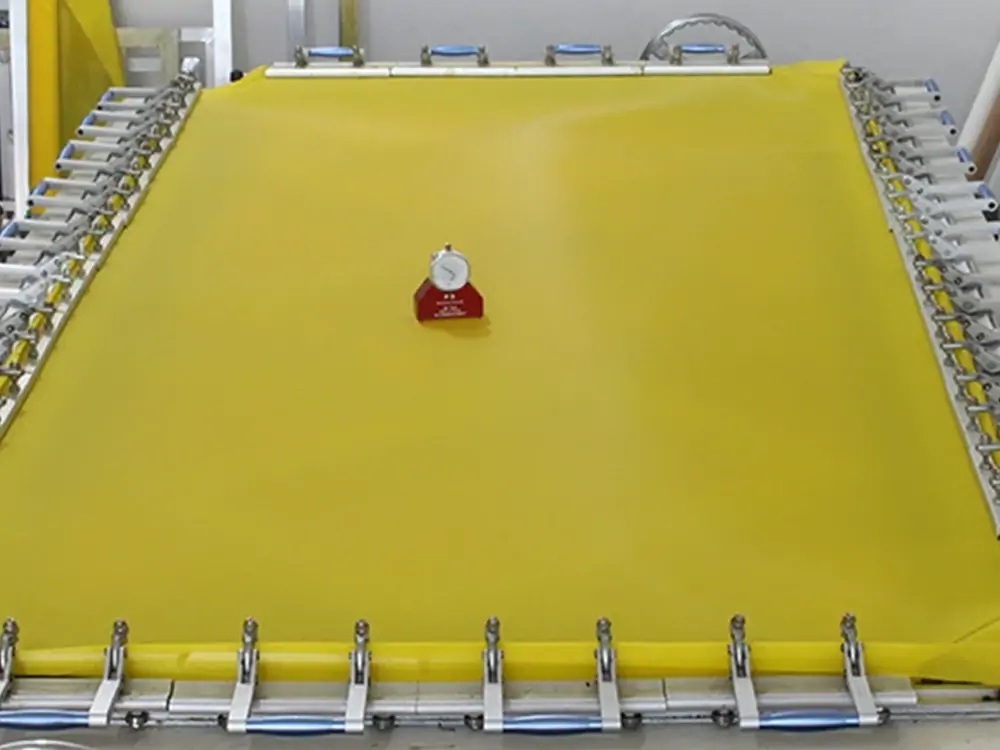
The Role of Screen Tension
Printing on cylindrical surfaces can be tricky. They are not like flat substrates. We take this opportunity to explain some of them. Curved screens on curved surfaces work. They must translate the screen to apply ink uniformly along the curve. Correct screen tension comes into its own as the deciding factor here.
Uniform Ink Transfer:
When printing, the correct tension keeps the mesh parallel to the substrate. If the work on the artwork is inconsistent, the ink might gather in one spot. At times, it may not transfer correctly.
Design Precision:
If the tension is not enough, the mesh will droop, which will, in turn, cause print blurs or distortion. High stress can distort the design by tightening mesh lenses, especially around details or preformed patterns.
Durability and Reusability:
Properly tensioned screens last longer. They need less replacement. Thus, the screen tension of cylindrical printing should be set to achieve maximum performance. The next chapter will illustrate this theory with simulations.
The main challenge in cylindrical screen printing is to find the best screen tension. It may vary by application. But the average screen tension should be 20 to 25 Newton centimeters. The range is needed to stabilize ink pick-up on curved, cylindrical surfaces.

Specific considerations regarding ideal screen tension depend on several factors, which include:
Ink Type:
Solvent-based inks might need a bit more tension. This will prevent the ink from dyeing the entire mesh. Aqueous inks may need average tension to flow well on the substrate. This will prevent overheating of the surface.
Mesh Count:
A higher weave (200-300 per inch) may need higher tension to keep precise fabric details.
Loose weaves with smaller numbers of threads per inch (for example, 110-160) accommodate massive inks at greater ease.
Substrate Material:
Again, tighter tension is desirable for sharper prints on glass or metal.
For softer materials like plastic or rubber, lower the tension a bit. The material may warp, or pressure can cause issues. Adjusting these parameters gives printers the best screen tension for their tasks. Screen tension is the total pressure a patterned screen exerts on a wafer during photolithography. It is essential to know that getting the right screen tension is a process. It starts with preparing the screen and continues with maintenance.
Here are some tips to help maintain optimal tension for cylindrical printing:
Use a Tension Meter:
A tension meter is a uniquely vital analyzer to measure screens’ tension. The period exchange retains tension for printing and eliminates fluctuations.
Choose the Right Screen Frame:
Aluminum or steel frames are most suitable because they enable constant tension to be sustained for extended periods. Wooden frames may give way or relax much faster than metal frames.
Tension the Mesh Properly:
While stretching for the first time, ensure the mesh is pulled with equal force and even tension on all sides. Failure to apply uniform tension creates areas of tension variation, affecting the final print to have the wrong shape.
Appearance:
The mesh could fail to maintain the required tension due to wear or repeated utilization over a particular period. Tightening the mesh now and then keeps it in good shape. It also prevents complications from varicose veins.
Store Screens Properly:
Screens should also be controlled. Extreme dryness or humidity can affect their tension when not in use.
Typical Issues That Arise from Mistaken Force
When the screen tension is wrong, it causes print faults. They reduce the quality of cylindrical screen printing. Below are some common problems and their solutions:
Too Low Tension:
- Defects: Getting some black smudge on the surface; some drawings or prints are partial at the edges; ink coverage is not all over the print.
- Solution: Progressively add the tension and use an anxiety ruler to check for the changes.
Too High Tension:
- Defects: Mesh damage, design distortions, pressure on the substrate, or other forms of distorting stress.
- Solution: Relax the tension in the system so that the mesh is not pulled taut during the setup.
Uneven Tension:
- Defects: Low-quality ink deposition and poor resolutions affect the prints in some areas.
- Solution: See if you have even tension across the screen, then re-stretch the mesh where necessary. If these problems are controlled, printers can produce high-quality cylindrical screen printing projects.
Conclusion
A key issue with screen printing cylinders is the screen tension. It must be correct for the best print quality. They refer to their effects on print quality, ink transfer, the screen, and the design. Your printing business will do best if you know screen tension, use the standard tension (20-25N/cm), and care for and replace screens. We need a good tension meter, durable screen frames, and precise cylindrical screen printing equipment. They are as important as their technical aspects.
At Once-Tech, we invite businesses to explore our cutting-edge printing innovations. Our advanced services are designed to elevate your printing capabilities.
We offer state-of-the-art Automatic UV Screen Printing Equipment and a variety of cylindrical screen printers that deliver exceptional performance. Our equipment is engineered to meet the diverse needs of our clients, ensuring high-quality results every time.
Discover how Once-Tech can transform your printing processes and help your business thrive!
Use the right tools and techniques to get the best cylindrical screen printing. Also, maintain the equipment. Keep at it until you get it right.