Introduction
To boost product packaging and brand visibility, a business should opt for a quality multicolor screen printing machine for silicone sealant tubes. Silicone sealant tubes have wide applications in the construction, automotive, and DIY industries. High-quality printing helps companies create better products. This sets them apart from competitors in the market.
How can you select a machine that offers excellent print quality and meets your production needs? The guide shows key factors to consider. These include machine selection, cost estimates, and how well it operates. The identification of requirements stands vital for silicone sealant tube printing operations.
Characteristics of silicone sealant tubes
These materials need specialized treatment to achieve proper ink adhesion on smooth surfaces.
The main technical attributes of silicone sealant tube products include:
- The material is either PE or PP plastic, but the surfaces need treatment for proper ink adhesion.
- Producers make tubes that have diameters of 30 mm to 50 mm. These tubes range in length from 150 mm to 200 mm.
- The printing must be durable. It should also be waterproof and scratch-resistant. This is important during storage and handling. Practitioners prefer UV-cured ink. It dries rapidly and produces durable prints.
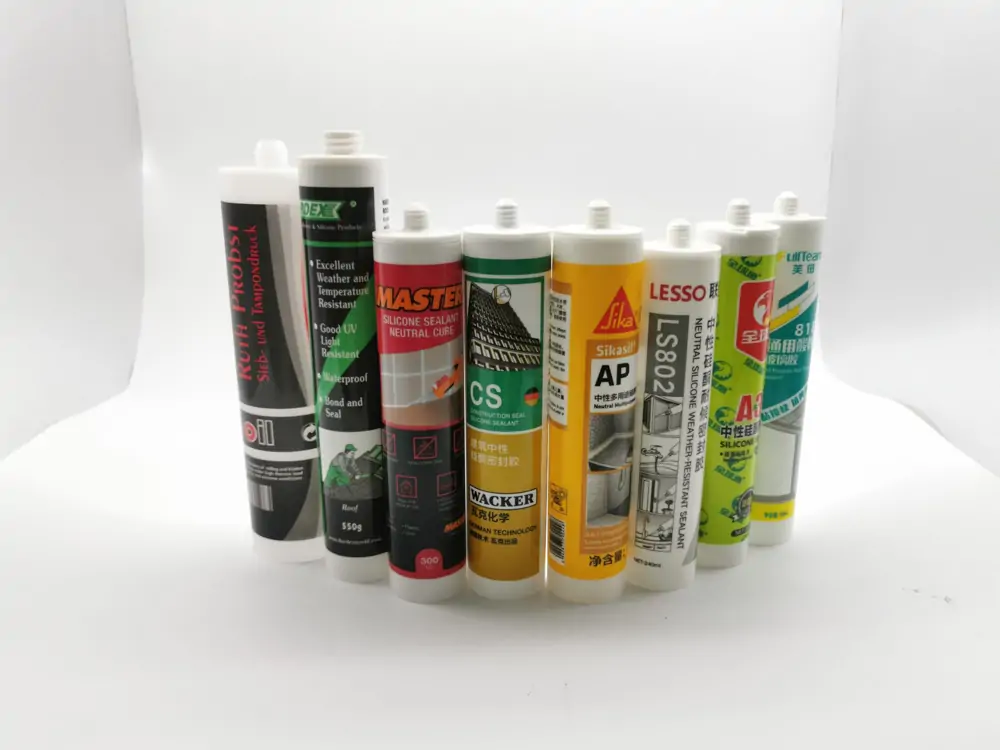
Benefits of Multicolor Printing
Multicolor printing presents many benefits that help businesses in their operations.
A product stands out because of its bright branding. This helps consumers spot it quickly.
Different application sealant variants can be designated as colors through market differentiation practices.
Using multiple colors in commercial printing makes the product look more expensive. This is achieved through high-quality printing.
Key Factors to Consider When Choosing a Multicolor Screen Printing Machine
Number of Colors
The first element for choice involves selecting the colors needed in your design. Screen printing machines come in different types. Some support two colors, while others can handle four, five, or even eight.
- 2-Color Machines: Suitable for basic logos and simple designs.
- These machines use four colors to create clear images and brand elements.
- High-end applications require screens with five or more colors. This is because they need precise color accuracy for advanced designs.
The fully automatic AP-100-5C can print in five colors. This allows for high-quality printing on silicone sealant tubes.
Level of Automation
Every printing operation requires attention to how much automation the equipment will perform.
Fully Automatic Machines:
Best for large-scale production. Automated features boost speed in operations.
The conveyors are used for:
- Auto feeding
- Flame treatment
- Screen printing
- UV curing
- Auto outfeed
Traffic-hazy printing capability assists firms in expediting their significant order completion times.
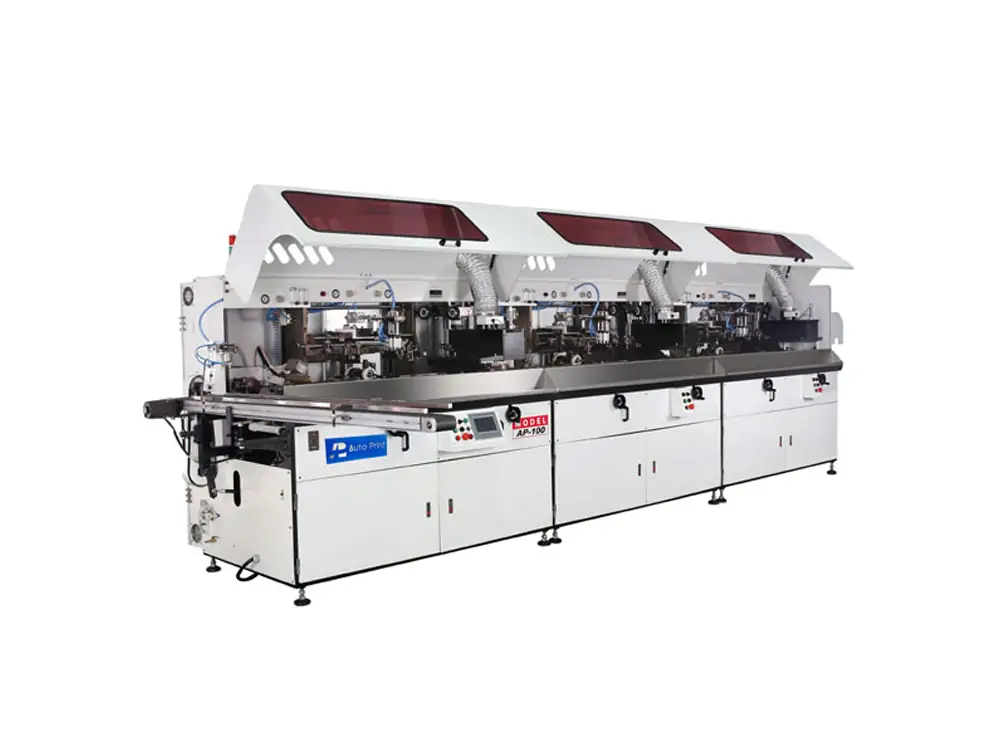
Semi-Automatic Machines:
These systems require manual help to operate. However, they are still a good choice for managing limited production capacity.
- The price of semi-automatic machines stands lower than that of fully-automatic machines.
- Businesses needing top operational performance should get a fully automatic machine. It will be their best investment for efficiency.
Compatibility and Size Range
The system limits its capability to process every available tube dimension. A machine’s selection should be based on the dimensions of your product tubes.
The machine should enable users to change its fixtures to handle various sizes.
The machine needs the capability to accept cylindrical-shaped items, including silicone tubing.
UV Curing Technology
UV curing is a crucial component that modern screen printing machines must feature. UV technology enables ink to dry instantly, making it resilient against damage and water exposure.
Advantages of UV curing:
- The printing process completes within seconds despite taking several hours before machine technology advancements.
- UV-cured ink maintains longevity because it lasts longer under changing environmental heat and moisture conditions.
- The accelerated drying speed enables businesses to run their production sequences faster.
Precision and Registration System
- Perfect alignment is necessary to print more than one color. Poor-quality prints and wasted materials can result from any misalignment.
- It also has optical sensor registration machines that guarantee that every one of the hues is printed at the correct spot.
- Choosing a machine with a 100% register system is better. This helps reduce errors and keeps quality high.
Cost and Budget
- The machine you choose will depend on your budget. The price varies from several colors, with some extra automation, to other little features.
- Lower cost but fewer features than entry-level machines.
Balance: Mid-Range Machines – Affordability mixed with functionality
- These machines are fully automated and packed with advanced features. They are made for mass production, like high-end machines.
- Premium machines require a more significant initial investment. However, they offer better efficiency and reduce long-term costs.
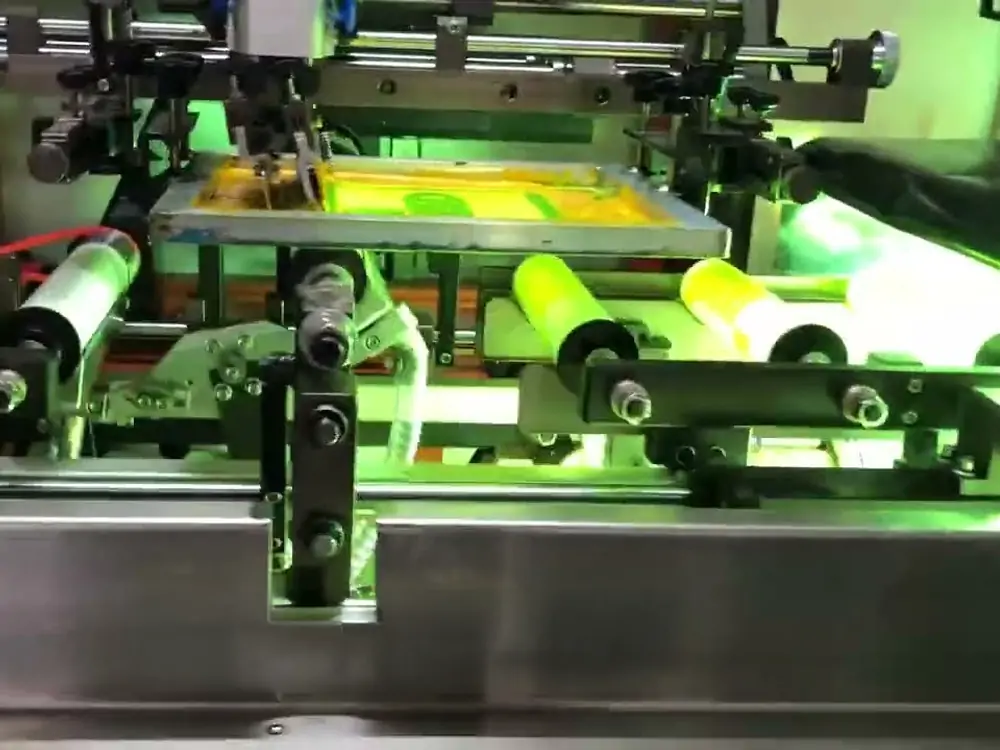
Recommended Machines and Features
Here are some top machine recommendations for silicone sealant tube printing:
Featured Model: AP-100-5C
- High-speed printing using a five-color, fully automatic printing machine.
- It’s a UV curing system that fast-dries and is durable.
- Ideal for large-scale production of silicone sealant tubes.
AP-100: Entry-level semi-automatic machine for startups
We offer mid-range machines – 3–4 color automatic machines for businesses that want to scale production.
Customization Options
Some manufacturers also provide custom fixtures to fit specific tube sizes.
You may consider the sources of installability and the technical support after sales.
Practical Tips Before Buying
Before making a purchase, follow these steps to ensure you’re choosing the right machine:
1. Test Samples
Request printed samples from suppliers. This will help you check the print quality, color accuracy, and durability.
2. Check Lead Time
It will help to understand how long it will take for the machine to be delivered and installed to avoid production delays.
3. Evaluate After-Sales Service
Check for suppliers of good customer support (spare parts availability, etc.) and technical support.
4. Compare Multiple Suppliers
Don’t just focus on price. Take that machine’s function, user convenience, and reliability over the years.
Frequently Asked Questions (FAQs)
Q1: How long does silicone tube printing take to dry?
A: All ink dries in seconds with UV curing. This may take hours for traditional methods of drying.
Q2: How much does a multicolor screen-printing machine cost?
A: Prices vary. Single-color machines often cost 20% to 50% less than multicolor machines. The exact price difference depends on features and automation levels.
Q3: Which machine suits a small business best?
A: Choosing a 2-3 color semi-automatic machine will be a good start if you operate on a small scale.
Conclusion
Picking a silicone sealant tube for a multicolor screen printing machine can be challenging. Consider these factors: color capacity, automation level, UV curing ability, and cost. Each aspect plays a significant role in your decision. The best investment balances a budget with production needs.
Contact Once Tech for details on top-quality printing machines supported.