The plastic cup printing machine is vital for cup and bottle printers. This sophisticated system holds tremendous operational importance for sustaining production and print quality. However, the company needs constant care to work well like most machines. Neglecting maintenance causes costly repairs, wasted time, and shorter equipment lifespan. It’s also good practice to purchase a strong, durable machine such as one from Once-Tech.
You must know and follow the maintenance policies for your plastic cup printer, regardless of your experience with it. They will help your machine run for many more years.
Daily Cleaning: A Non-Negotiable Routine
The first and most critical aspect of maintenance is always to keep your machine clean. In a short time, ink deposits, dust, and debris may spread in the machine. They may cause paper jams, low-quality prints, and uneven ink.
- Print heads and rollers: Always clean the heads and rollers after each shift or run to avoid ink buildup.
- Ink Trays and Nozzles: Clean the containers and nozzles more often. Paper or cloth can block them and slow the ink flow.
- Conveyor Belts: Clean conveyor belts. They may contact the foil and cause ink blots or other damage.
- Pro Tip: Always use cleaning solutions that won’t harm your machine’s fabric. They can affect delicate parts of the machinery.
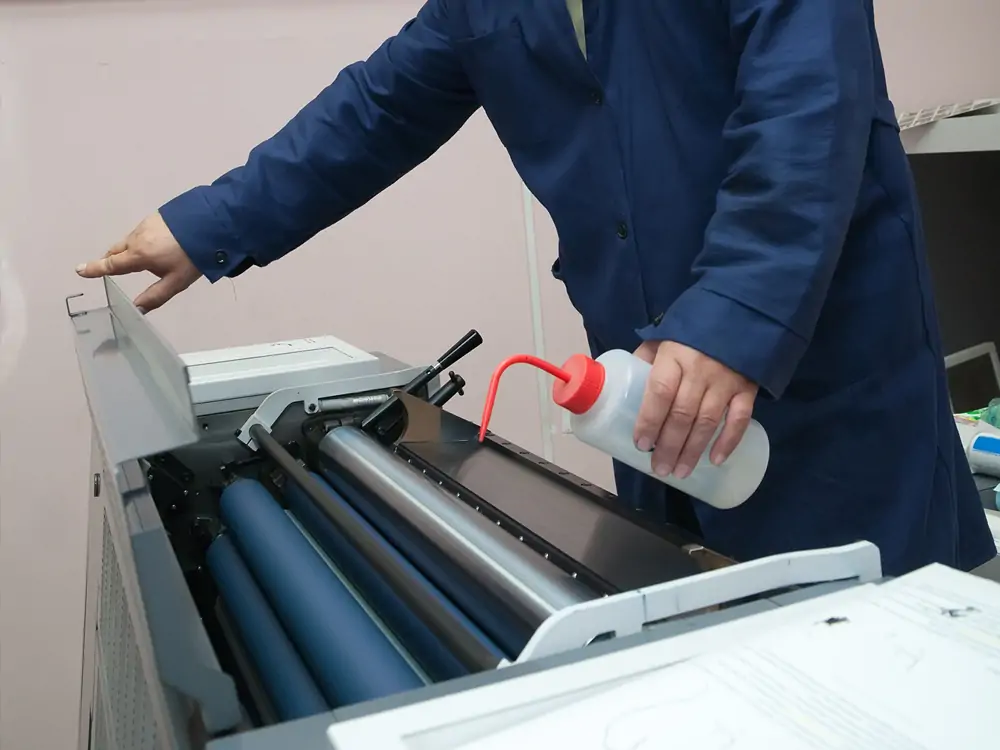
Lubrication: Keep the moving parts happy
I found that plastic cup printing machines have many moving parts. They have gears, bearings, and chains. They must be oiled to work well. Grease and oil are, in effect, gone. The engine is not lubricated. Constant friction wears out the parts. This can cause a breakdown or a greater need for replacements.
Frequency: Grease all moving parts at least once a month or as the manufacturer specifies.
Lubricant Type: Use high lubricants that suit the machine’s materials.
If not lubricated, these parts tend to tighten. This causes friction, noise, and sometimes, mechanical failure. This will ensure the motor runs with low wear. It will also produce a smooth, quiet sound.
Supervise and Sustain Air Delivery Systems
Most plastic cup printing machines are pneumatically operated. This applies to applying ink and moving parts that handle the materials. For accurate printing, the air supply must be clean and consistent. So, this is vital if you use compressed air on your machine.
Check Air Filters: Wash the filters. Blocked filters prevent proper airflow through the machine and equipment.
Monitor Pressure: Check the air pressure and set it right. Low pressure can affect the printing parts.
Tip: Air leaks or contamination cause poor machine performance. So, check air hoses and fittings for wear or leaks.
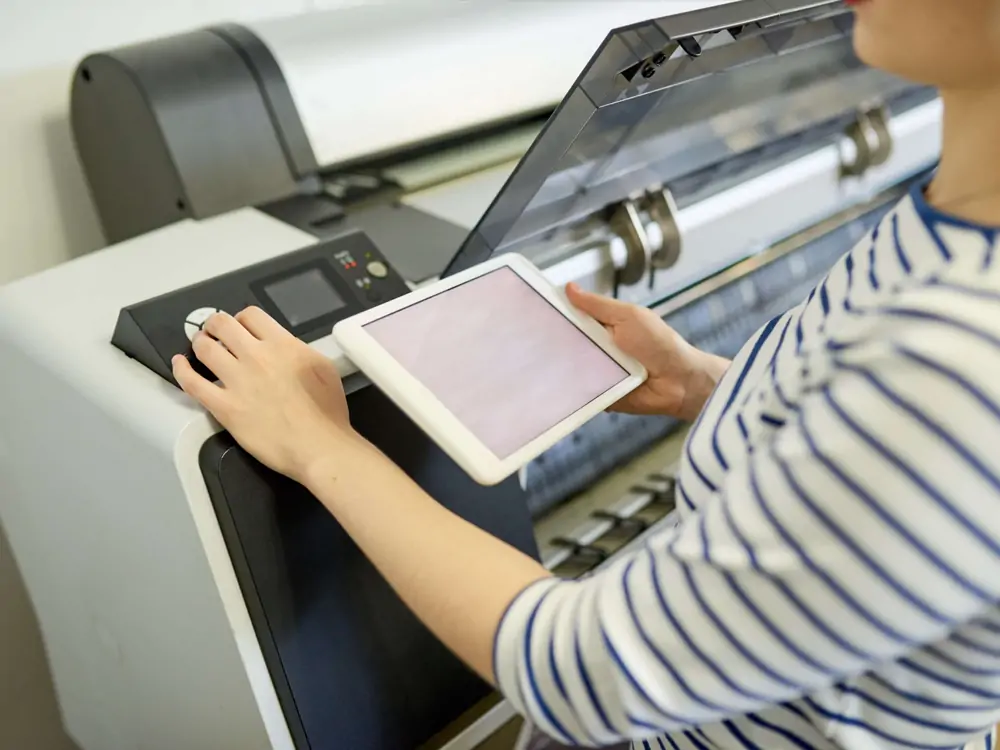
Do it daily or weekly to ensure that the prints are precise.
So, the printer needs fine-tuning to produce high-quality prints. Faulty alignment or bad settings will cause blurred images, smudged ink, or off-center designs. Calibrating the machine will ensure that ‘templates’ match and prints are the same size.
Inspect Settings: Adjust the machine settings if needed after the extensive run. This refers to the position of the print heads and the pressure the squeegee and the cup holders apply.
Advice: Check the document’s calibration settings for different materials and print types. They can be fixed and used when shifting between production runs.
Timely Replacement of Worn-Out Components
If you have not cared for the machine, its parts will wear out. They will need replacement. This is the secret to lengthening the machine’s lifespan. Worn-out parts are usually replaced before they cause severe damage.
Inspect Belts, Rollers, and Gears: Check for defects, like cracks or deformities. Also, check for low flexibility. Do this regularly.
Print Heads: If the print quality decreases, it is high time you change the print heads.
Pro Tip: Accumulate spare parts to avoid long-term losses when such parts have to be replaced.
Electrical Components: Supervise for Safe and Productive Operations. Electrical management includes almost all machine components. It controls the print head and the conveyor. If the electrical parts are damaged, they must be checked and replaced often. This is to ensure the machine is safe for the operator.
Check Wiring And Connections: Look for loose connectors, wrong cables, or oxidation. It is best to address these issues early. This will prevent short circuits and machine problems.
Test Sensors: Many checks must ensure sensors work and are accurate. Sensor malfunctions may change speed. In the worst cases, they may stop a machine.
Note: All work must be done by skilled professionals. This prevents accidents and further damage.
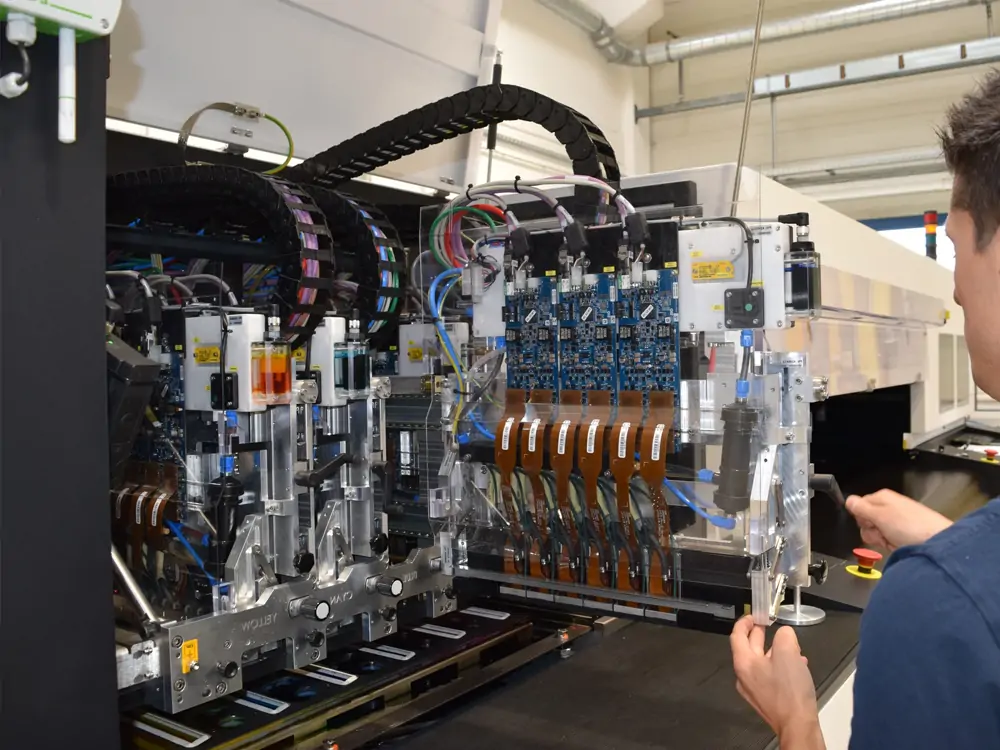
Software and Firmware Updates
Most cup-making printing machines today have software-controlled features. Updating this software is crucial. It will add new features, fix bugs, and improve performance.
Check for Updates: Visit your machine manufacturer or service provider for new software. It can improve the machine’s performance.
Backups: Always export the current settings. Updates may cause data loss or downtime.
Many users need to learn that new software versions may improve print quality. They can also extend the machine’s lifetime by fixing bugs and fine-tuning processes.
Professional Maintenance Booking
It is, however, recommended that professional servicing be done every six months or yearly. This is in addition to your daily and monthly cleaning. Only professional technicians can examine the machinery and its parts. They can find issues and failures and make the needed repairs.
Expert Inspection: It also means technicians can find hidden problems. Simple tests may not detect them.
Optimize Performance: Servicing lets you fine-tune your machine for peak output.
Tip: A log will guide technicians in finding problems while servicing a client.
Conclusion
Caring for your plastic cup printing machine goes beyond keeping it running. It’s about ensuring a good ROI, saving costs, and prolonging your printed products. Following these maintenance tips will minimize repair time. They will also provide quality prints throughout the machine’s life. Maintenance involves cleaning, greasing, adjusting, and replacing worn parts. It also includes professional check-ups. This can extend the life of your printing equipment.
Using pre-made maintenance measures will boost your business. They will extend the life of your plastic cup printing machine.